We have been boring lately. Though in general, most of the work of manufacturing is just grinding, on the supply chain as well as on our own engineering tasks. That’s one reason I was holding off on an update. The other reason is I was hoping to hit some more milestones to report back. Got mixed news on that.
Software
I’m doing a lot of work on the backend (that is, code running on a couple of servers in Dallas that coordinate the Pickup device, the Pickup web app, and act on the sensor data), getting the server processes working efficiently (theoretically a lot of Pickup data to store) and playing well with each other. There’s the MQTT broker, an open source program we use to route messages to and from Pickup. We have a program called Squirrel which packs away the sensor data you want to record, and another named Ferret which can quickly retrieve that data for you.
On the app side, I’ve been making it more resilient against network outages. Not quite offline-capable yet, but work that will pay off in the long run. And working on data visualization.
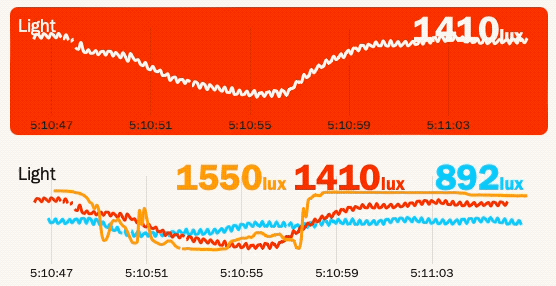
Here’s a multichannel graph displaying light levels from three different Pickups. (Two of them have noise in the signal caused by LEDs that are blinking for debugging purposes.)
Electronics
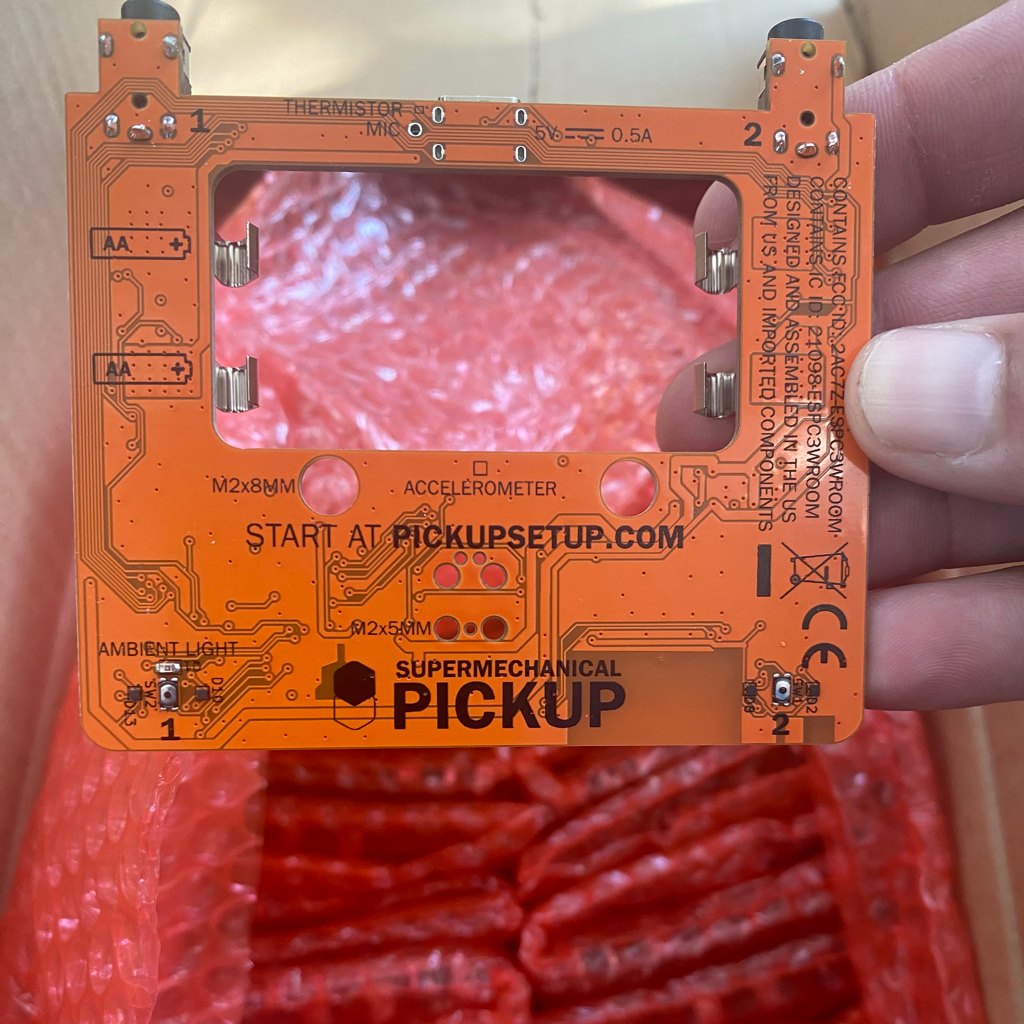
Okay, one milestone was hit. We got the first 50 production boards this week. The custom board color came out nice. I just realized that they’ve gone from green to yellow to orange, and soon will be dropping off the production tree.
My initial mechanical check shows that all the issues (notably the concerns we had about the battery clips’ soundness) have been solved. However, this was done with the existing final printed prototype, and there were a few changes made to the plastics since then. All of those changes should only improve things, but you never know until you put them together.
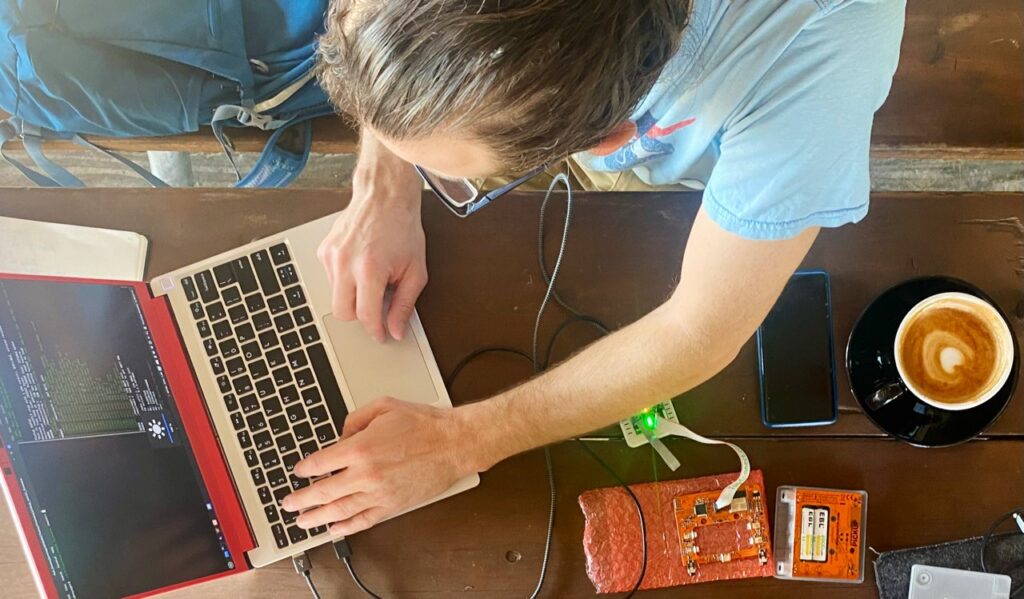
Here Jeremy’s running a hardware test on one of the boards. It passed without issue, and he’s going through the rest now. This batch is also an opportunity to verify our test processes, as described in the last update. So far all the boards are passing, and he’s refining his test code so he can send it off to the assembler to run it on the main production run so they can catch and fix problems before shipping us bad boards.
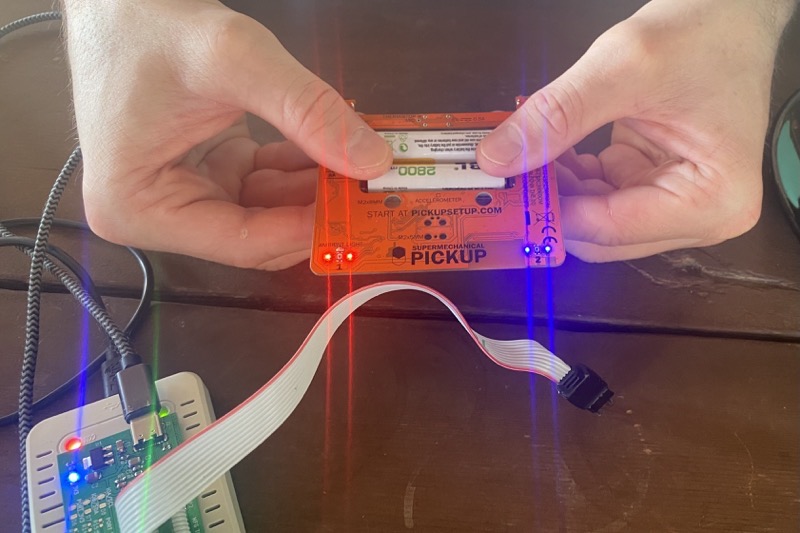
And now with the basic server running, Jeremy’s making final design changes to the firmware to support that, and then we can start on some of the final module designs and use our own system to collect data and verify everything is working the way it should.
The takeaway is that the mainboard design is stable, our board assembler did a good job, and any changes now are only to make production easier. These boards should be going to some of you when we get cases.
Mechanicals
Speaking of, the plastics remain a thorn in my side. The molds still haven’t been finished and so I don’t have first injection molded parts to approve. At some point, the mold maker got impatient with my iterative changes and pushed us back in the production queue. Last week we were told that the molds were going to be started this week, which could mean first items by the end of October, but I’m waiting to get confirmation. Doesn’t help that this is being relayed through the injection molder, who has the direct relationship with the mold maker—but probably for the best since the mold maker would be less motivated if we were directly interacting as a small first-time customer. It’s frustrating that I can only pester at this point. Welcome to hardware production.
Reading
I’m a product development sicko—I love to read a good hardware story, like taking the Fitbit from idea to product. And I just recounted the story of the first Apple computer to my kids (hey, they asked—future sickos). Any others? The simpler the product, the better.
No matter how simple of a product you’re making, the logistics of putting it together at quantity provides a bottomless well of details to consider. If you try to swim to the bottom of that well, you end up with The Toaster Project, which documents an attempt to make a mass produced object from absolute scratch.
I expect to have better news on plastics next time, as well as minutiae on the parts you don’t usually think about. Thanks for bearing with us through the process. Pickup will be better for it.
Crossposted from Pickup Kickstarter update #10